Can Housebuilders Forge their own Path Towards Net Zero?
10/10/2023
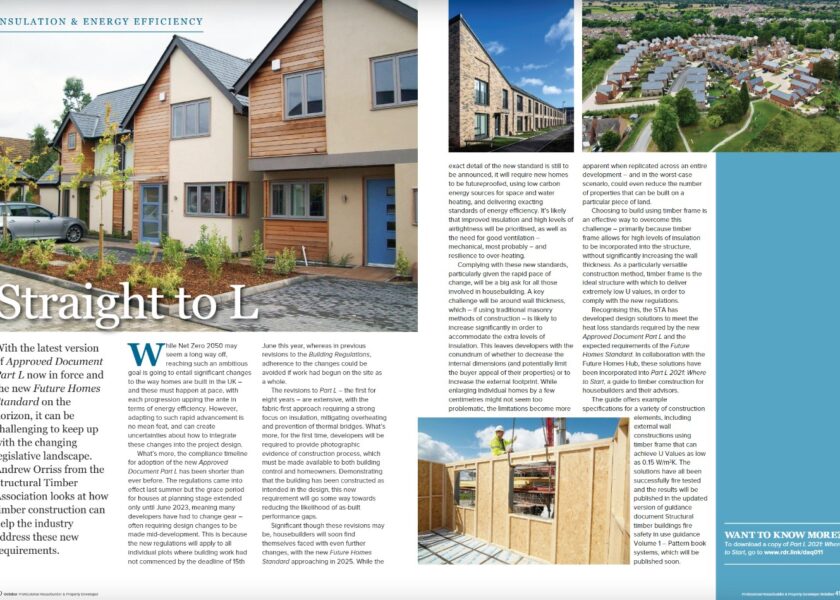
As critics warn that the Government is falling dangerously short of its climate change targets, Andrew Orriss from the Structural Timber Association urges housebuilders not to ignore the low hanging fruit that could speed up their own de-carbonisation journey.
Warning that little progress has been made in the past year, the UK’s Climate Change Committee (CCC) recently published its annual progress report to Parliament, concluding that it has ‘markedly less’ confidence that the UK can meet its climate goals from 2030 onwards compared to in its previous report. Calling for urgency and a stronger sense of leadership, the report emphasises low carbon heating and energy efficiency measures as the principle means of tackling the housing sector’s carbon contribution.
For housebuilders, it’s clear where priorities are being directed then – yet it seems that a key opportunity is being missed here. It could be argued that the Government’s policy of steering housebuilders towards a focus on building services and energy sources is a back-to-front approach, as operational CO2 emissions account for only a small portion of a home’s total carbon cost. Instead, shrinking the overall carbon footprint by reducing the embodied carbon of the materials used to build the UK’s housing stock could be considerably more effective.
While renewables, EV charging capacity and other low carbon technologies are clearly an important part of the mix when it comes to meeting housebuilders’ net zero obligations, choosing to build with structural timber is a quick-win way to significantly reduce carbon overall.
Indeed, the aforementioned CCC progress report does state that “timber in construction can both sequester carbon in buildings and displace the use of high-embodied carbon products such as steel and concrete,” but previous communications have gone even further than this. In 2019, the CCC found that if 270,000 new houses were built each year using timber frame, it would increase the carbon sequestered in UK homes to 3Mt. Currently, the use of structural timber in new homes results in the sequestration of a little over 1Mt of carbon per year.
In addition to helping housebuilders meet their environmental targets, opting to use structural timber systems within new developments can help to alleviate other pressures. On average, using timber frame systems can reduce build time by eight weeks, when compared to traditional masonry methods. This is largely because timber frame is manufactured offsite and delivered as prefabricated panels that can be erected quickly.
Furthermore, producing timber frame systems offsite improves reliability. Firstly, as they are produced in controlled factory environments, quality control is assured, resulting in fewer errors during assembly. Secondly, the fabrication of timber frame systems in a factory is not weather dependant, meaning build programmes become far more predictable.
Understanding both the environmental and structural benefits that timber presents, the question is why are more housebuilders not taking advantage of it now? Ultimately, the answer to this relates to culture. For example, the Scottish market is by far the most developed within the UK when it comes to the use of timber frame, and has a long tradition of using the material. According to an NHBC HMI Report in 2019, 92% of homes in Scotland are built in timber frame, equating to around 23,000 units. While that percentage is significantly lower in England at just 9%, the volume of units does not have the same disparity, with almost 14,000 homes being built in timber frame.
The more recent NHBC HMI Report in 2022, states that “in Scotland, it is becoming increasingly rare to see any other form of production than timber frame.” Yet, the trend shows an absence of any significant uplift in timber frame in England – which is surprising, given the desire to see work shifted off site.
However, this may not be the case for much longer. Taylor Wimpey’s recent announcement of investing in its own timber frame manufacturing facility in Peterborough means that the three largest housebuilders in the UK now possess in-house manufacturing capabilities. Additionally, Barratt Homes has made investments to expand the capacity of the Oregon Timber Frame facility in Selkirk, while also establishing a new manufacturing site.
In one of the more recent developments, CALA Homes has acquired Taylor Lane Timber Frame, and has stated that the purpose of obtaining the business was to “progress towards their sustainability targets and support delivery of the group’s ambitious growth plans in the South of England.” These developments serve as a clear indication of the advantages that timber frame construction brings to the UK housebuilding industry, enabling efficient delivery of housing at volume while meeting carbon reduction requirements.
What’s more, although the Government might be steering in one direction, it’s important that the housebuilding industry recognises that it is not obliged to follow this line of travel. Indeed, as long as regulatory requirements are met, it is able to forge its own path in delivering better quality and greener housing. After all, why wait for Government thinking to catch up when timber solutions are ready now, offering a quicker, more reliable and more sustainable solution to the climate crisis?
To read article click here