Richard Whittaker at Citizen Housing talks to STA
30/08/2023
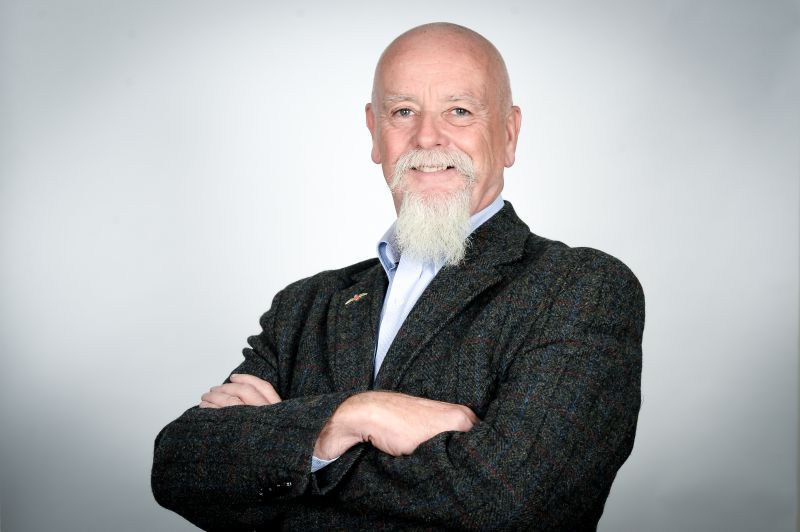
The STA sat down to talk with Richard Whittaker, Director of Development at Citizen Housing about the affordable housing industry, and the role timber has to play in the housing crisis.
Can you provide some information about the Citizen Housing Group and the types and volume of housing being built?
Citizen Housing is one of the largest landlords across the West Midlands with approximately 30,000 properties in our portfolio. We have an ambitious development program to help combat the housing crisis and our goal is to deliver over 2,800 new homes between now and 2028. We’re determined that these will be high quality affordable homes and, for the first time in my career, we are delivering affordable housing to a higher standard than open market sales, and that is a real credit to the organisation and our direction of travel.
The UK still faces challenges due to the housing crisis, with an average tenancy length of around 7.5 years compared to 22 years in Germany. Citizen Housing aims to make value-driven judgments to improve housing standards and adaptability for our customers to promote longer more sustainable tenancies for our customers.
For that reason, we build houses of various sizes, including larger ones for families with 4 to 5 bedrooms, as well as bungalows to help people downsize and free up family-sized homes. In addition to houses, we construct apartments, and supported living accommodation.
In terms of the adaptability you mentioned, would this extend to futureproofing homes built by Citizen Housing?
We already build to the Lifetime Homes Standard, which is the regulation in place. However, we also have started to adopt the Future Homes Standard (FHS), or at least, our interpretation of it.
We actually conducted a pilot project in which we constructed two houses to the Future Home Standards in the place of a derelict Scout hut. The homes were designed and built to improve useability and energy efficiency, and overall, the project demonstrated a significant reduction in energy costs. Due to a fabric-first approach to insulation and the use of low carbon technologies like air source heat pumps and ventilation recovery systems, the total energy bill at that time was £600 measured over a 14-month period and included the removal of a dirty energy solution with the omittance of gas.
To reduce the impact on the local community during construction, we used a light steel modular construction, which resulted in a reduction in our carbon footprint with fewer deliveries. As a charitable organisation, there is a balance to strike between the need to invest in higher standards with the goal of accommodating the large number of people on our waiting list. We are always seeking efficiencies in the specifications and delivery methods of our buildings, and we encourage the industry to identify cost-saving measures through the use of modern methods of construction and factory-based approaches. Ultimately, Citizen Housing promotes collaboration and joint ventures with developers and supply chain partners to accelerate construction and deliver more affordable homes.
How many of your homes are built with Structural Timber?
Currently we are forecast to deliver 674 homes f this year, but through our participation in a strategic partnership with Homes England, we have made a commitment to ensure 20% of our programme will be constructed with a Category One or Two MMC solution, which is essentially a pre-manufactured modern method of construction. That absolutely lends itself toward the use of timber frame and open and closed frame structural insulated timber panels. Between now and 2028, we expect to deliver 500 of the aforementioned 2,000 new properties, in timber to ensure we take advantage of the sustainable and the environmental benefits of timber.
What do you see the barriers are to choosing and building with structural timber for Citizen Housing?
I believe one of the barriers is the term ‘modern method,’ which is not entirely accurate. There is a timber frame building still around that has existed in the UK from as early as 1270, which is a surviving example in Hertfordshire. Timber is a highly usable and flexible material, and in my experience, the challenges arise when people adopt a different build method without treating it as distinct from what we are accustomed to.
It’s essential to acknowledge that modern methods of construction require modern methods of delivery. This aspect is often overlooked, affecting quality management in both factory production and on-site construction. Additionally, we operate in a high-pressure, competitive environment. Once developers find a successful build model that manages risk and ensures viability, it becomes challenging for them to change it. To encourage adoption, there must be a clear focus on benefits, and understanding. The Structural Timber Association has made strides in supporting this with their STA Assure Scheme, recognised and adopted by warranty providers, providing clients with the necessary comfort to pursue these methods. However, there is still a gap between us and the developers, though a significant number already recognise and utilise modern methods, with around a 92% adoption rate in Scotland.
As you alluded to earlier, the early collaboration with those partners as well must be key to ensuring a smoother delivery?
When we use timber, we always collaborate with experienced developers familiar with timber construction. One of our primary considerations is whether they are STA members and the level of their quality assurance framework. Once we confirm their membership and standards, we can rest assured that they have already met critical benchmarks. This ensures that we are not taking any chances with the timber solution, as they have invested in attaining the necessary competency and understanding to deliver a reliable and worry-free project.
How can the government and the timber industry assist with increasing the use of structural timber in construction?
For the timber industry, it’s crucial to continue promoting the use of timber and maintaining high-quality assurance standards. One aspect that needs improvement is the level of promotion throughout the industry. The positive impact of timber doesn’t seem to reach as many people as we would like. Creating more awareness and sharing success stories can help with broader understanding and appreciation.
Regarding the government’s role, it needs to continue to review and develop building regulations to ensure that the performance standards of our construction not only reduce our carbon footprint but also provide cost-effective solutions for our occupiers. However, it’s currently challenging to depart from the minimum standards set by regulations, considering the competitive market and uncertain client preferences. But that is a challenge Citizen have embraced.