Project: Brian & Margaret, Scotland
Company: Scotframe
Sector: Self Build
Technology: Timber Frame
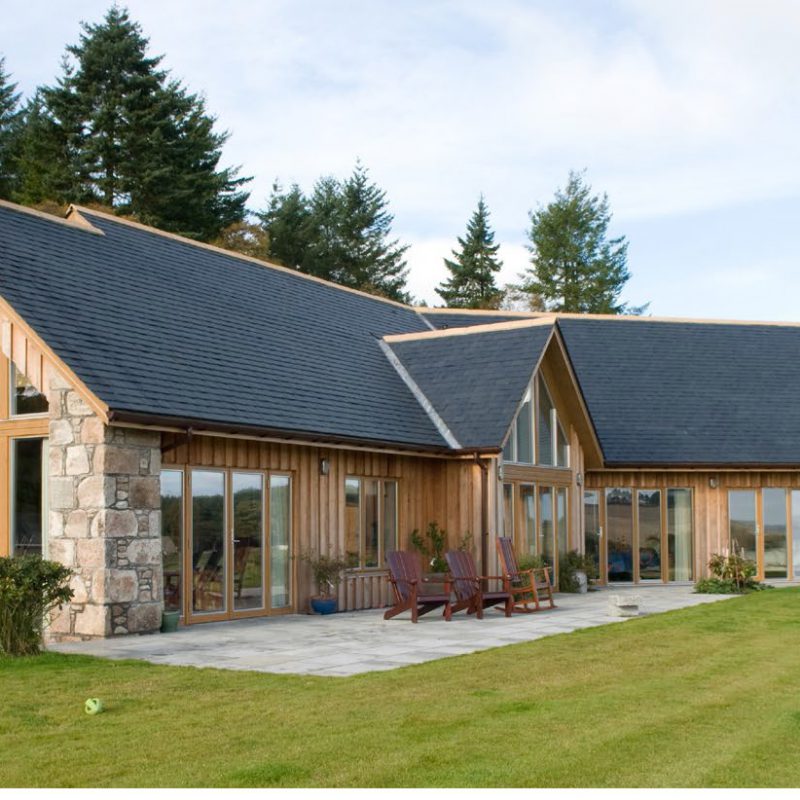
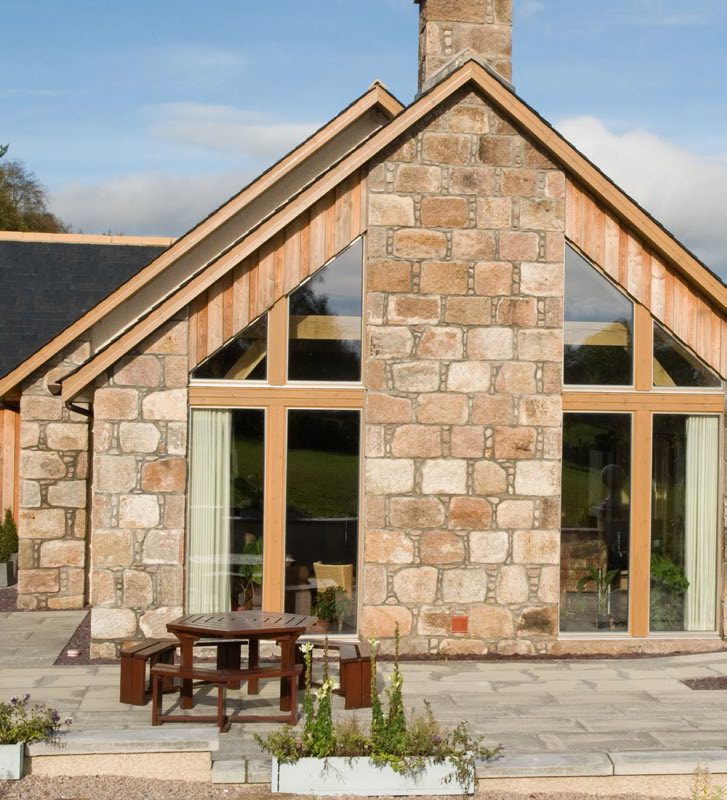
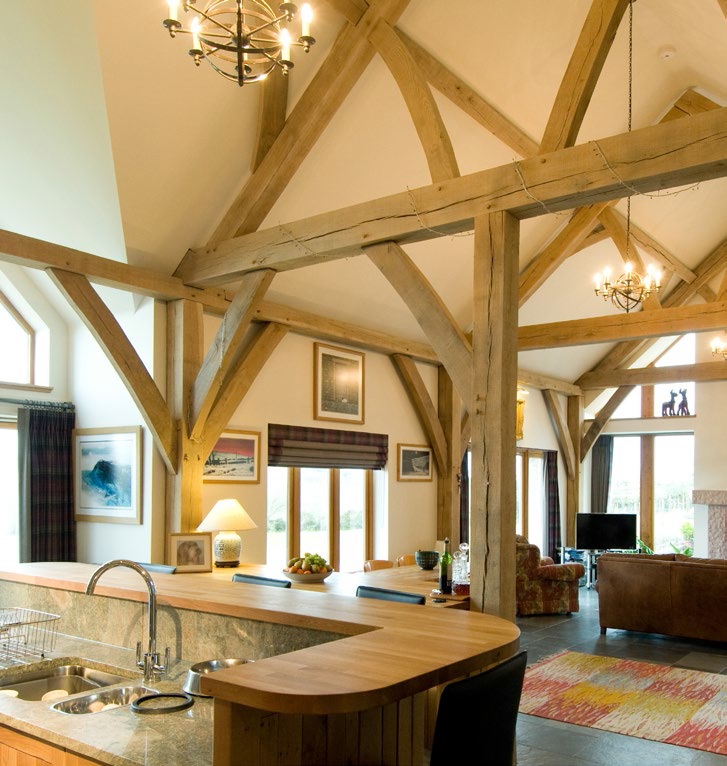
Overview:
In the beautiful Aberdeenshire countryside, an old estate cottage becomes a stunning new home it was a case of location location, location for Brian and Margaret Garden when they turned to Scotframe, the UK’s leading full kit timber frame manufacturer and supplier, to build the home of their dreams in the beautiful Aberdeenshire countryside.
The plot they found was a real prize, as sites in the lovely rural area are rarely available. Oil technology professional Brian and Margaret, both in their fifties, knew at once it was the home for them. Their site contained an old estate cottage and, though the couple had undertaken home extensions in the past, they knew at once that it would not be viable to extend the cottage – and that, because the design they wanted was so unique, self-build was the only option.
Project Type/Application:
However, in keeping with their environmental ethos, they retained all the Aberdeenshire granite from the demolition of the cottage and re-purposed it, with the aid of a very skilled local craftsman, in the new house. “It was a labour of love,” said Margaret Garden. “We knocked the cottage down ourselves and lifted every stone in the building. We now know it very well.”
What made the building very unusual was an existing architect-created oak frame, around which the stonework had to be erected. The Gardens were insistent that insulation had to be of the highest quality and chose Scotframe’s Val-U-Therm® panels, with very low U values, industry-leading insulation, air tightness and thermal performance.
Margaret said: “We are very environmentally conscious, and this was a one-off opportunity, so it had to be right. We also have a bio-mass boiler for hot water and heating, so the house is very sustainable.
“The Val-U-Therm® panels also feature a service void for wiring and pipes, so it is very easy for the builders. But when they were in place, it was remarkable. Every new build house has to have an air tightness test and the man who did ours could not believe the levels we had achieved.”
Outcome/Results/Success Factor:
Obtaining planning was a long process but, as Margaret said, “it is a very protected area and the planners were right to be stringent”. Again in keeping with their principles of localism, all the tradesmen involved in the build, from the joiners and builders to the plasterers and painters, came from within a 10-mile radius. “It was very important for us to put the money for the build back into the local economy,” said Margaret. The quality as well as the service was truly outstanding. “Their engineers had to work closely not only with our architect, but with the architects who were responsible for the oak frame. They had to build round it, but they worked excellently together, liaising at every stage to make sure the job was to our – and to their – satisfaction.”