Project: Roger Burton
Company: MBC Timber Frame
Sector: Self Build
Technology: Timber frame
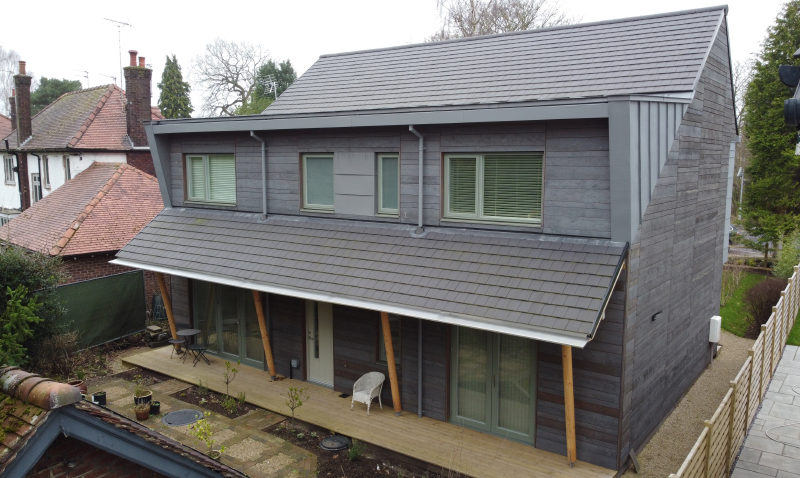
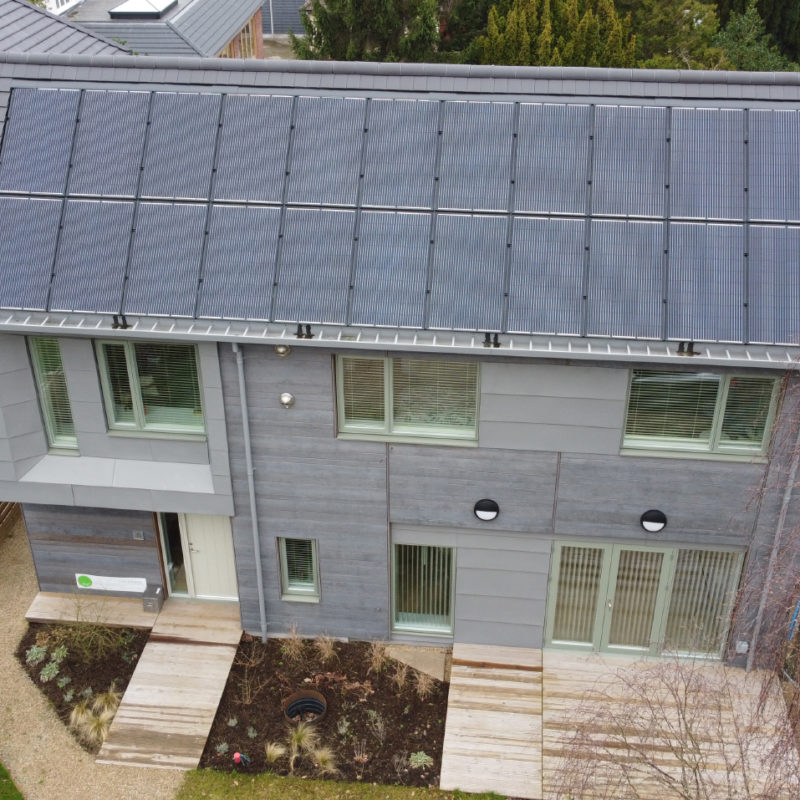
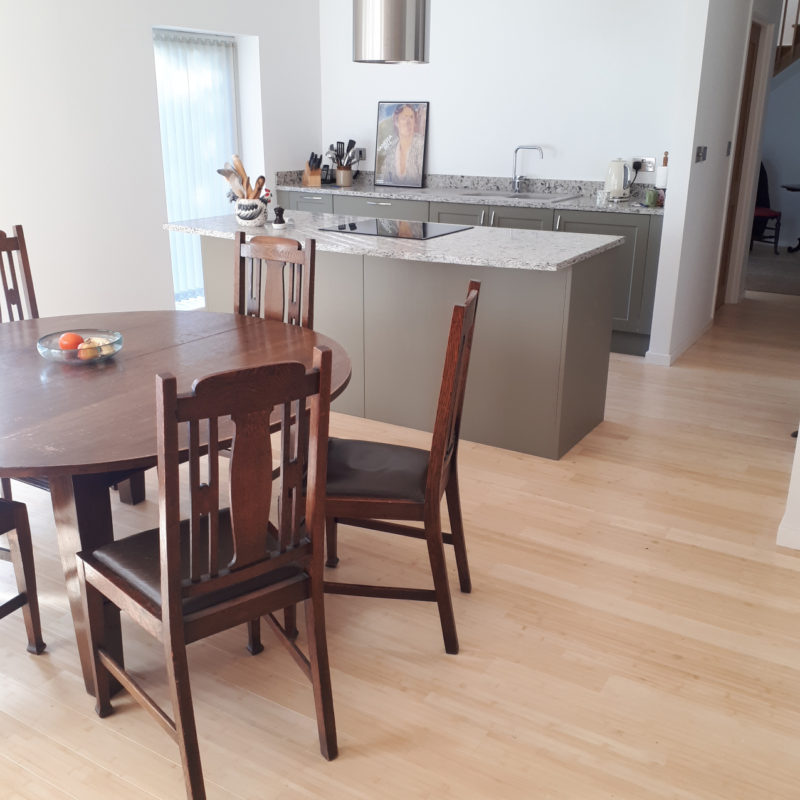
Having spent more than 40 years practising as an Architect, specialising in the low energy design of a range of buildings including hospitals, health centres and schools and, more recently, one off, high performance residential dwellings, Roger Burton looks back on his career with a wry smile as he recalls setting out as newly qualified architect with the ambition to one day build his own “highly energy efficient” home.
Roger has developed a career long passion for low energy design, environmental sustainability, construction quality and building performance, and has spent much of his career working with clients and extolling the benefits of passive design and energy efficient construction, what we now might call Low Carbon design. It was a discipline originally aligned towards building occupiers in the Health Sector who needed high performance buildings which would, over their lifetime, prove to be operationally lower cost to run than “the norm”.
“For me, choosing MBC Timber Frame to supply the superstructure of my new house was a reasonably straight forward one – they had a good offsite engineered system which met the desired U Values for the walls, roof and ground floor slab for my Passivhaus project as well as the quality of a product manufactured in a factory environment.
“Their timber frame panels use natural materials and recycled insulation which gives a high level of insulation, low ‘whole life’ carbon and low environmental impact.
“It was the inclusion of the thermally insulated slab for the building to sit on and the achievement of a tested, low air leakage and thus negating the need for a series of separate sub-contractors, which, as well as the timber frame panel construction method, confirmed my thinking,” he says.
Building to Passivhaus standards is a rigorous process requiring considerable attention to detail and Roger is happy that the exacting standards he set not only himself but also his suppliers have been met in his recently completed new home.
“Once the slab was completed the frame went up in less than two weeks and once windows and doors were installed we were ready for an air tightness test (achieving a commendable 0.33 ach ) and insulation which was blown into the continuous cavities in the external wall construction,” commented Roger.
In acknowledging that he is something of a perfectionist he is quick to point out that during his new home build process there were learning points which, whilst at the forefront of Low carbon design now, should and will become far more the ‘normal’ as self builders strive ever harder to reduce the “whole life” carbon footprint of their new home and we build Zero Carbon homes as a matter of course.
Roger’s new home, as any Passivhaus, has an extremely small heating demand and has no conventional heating system. This is an important step towards achieving a Zero Carbon performance. It is off the gas grid – an all-electric home with a substantial part of the hot water needs of the house being satisfied by photovoltaics. Its mechanical ventilation and heat recovery system was designed and installed by Roger and this contributes to the homes energy efficiency while providing continuous fresh, filtered air.
Roger’s four-bedroom home was granted “Certified Passivhaus status” from the Passivhaus Institute in 2021. One lifetime ambition achieved.